How Textile Industry Reduces its Water FootprintExplore how the textile industry reduces water at fabric mills with innovative dyeing techniques...
Published on by Water Network Research, Official research team of The Water Network
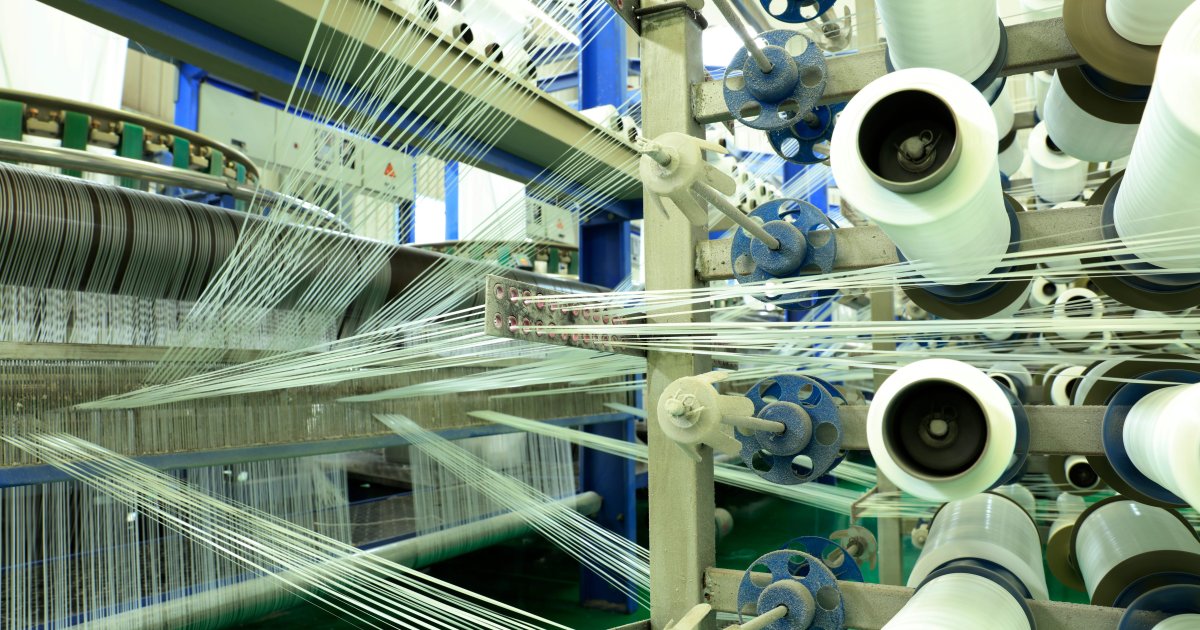
Explore how the textile industry reduces water at fabric mills with innovative dyeing techniques, recycling practices, and advanced technologies, leading to more sustainable and efficient production.
Louisa Smith AUTHOR:
All the Ways to Reduce Water in the Textile Industry at a Glance
- Understanding the Importance of Water as a Precious Resource
- Implementing Dye-House Rules
- Opting for Dope-Dyed Yarns
- Recycle Textile Waste – From Trash to Treasure (T-2-T)
- Exploring Water-Reducing Structural Solutions
- Leveraging Advanced Printing Technologies
- Considering Lab-Grown Cotton
- Promoting Water-Saving in Domestic Laundering
- Innovating in Footwear Manufacturing
01
Understanding the Importance of Water as a Precious Resource
The textile industry has always been a water guzzler with textile production requiring water for a variety of stages from preparation, sizing, desizing, scouring, bleaching, dyeing and printing. An estimated 93 billion cubic meters of water used, including cotton farming, annually according to Ellen MacArthur Foundation: A new textiles economy: Redesigning fashion’s future, but, as a more responsible and accountable industry emerges, the use of water is being reduced in a variety of ways.
Responsible textile mills also invest in the latest efficient dyeing machinery, signed to reduce the use of water. But there is a host of alternative developments happening, that are less reliant on traditional dyeing methods, leading to mass reduction in our water use, as well as cost savings.
02
Implementing Dye-House Rules
Colours
Cleaner dye chemistry aids water savings in today's modern dye houses
Image credit:Engin Akyurt/Unsplash.com
Recycling water and waste water treatment plants are the norm now in the textile mills that maintain strong sustainable values and a high regard to efficient manufacturing and use of resources.
Key among these is low liquor ratio dyeing equipment that significantly reduces water usage and energy-efficient, on-demand boilers that substantially reduce dye house emissions and the latest dyeing equipment that has a superior level of efficiency and reduced waste.
Looking to awarded companies at ISPO Textrends, it is clear to see the importance water savings have. Toread has introduced low-carbon dyeing technology, saving water and energy. CO2 dyeing involves using supercritical carbon dioxide, a state of carbon dioxide where it exists as both a liquid and a gas, as the dyeing medium. This innovative approach eliminates the need for water and reduces the environmental impact associated with conventional dyeing methods.
Synthetic dyes, have long superseded original dyes, with dye stuff providers developing cleaner chemical solutions for today’s colorways. Today natural dyes are making a return, predominantly with cellulosic fabrics, however Noyon Lanka, a subsidiary of MAS Holding, has launched Planetones, is the world’s first 100% natural dye solution, applicable to nylon, as well as cotton and wool materials.
A test comparison was carried out between Planetones and the traditional synthetic dye process, resulting with a water saving of 43 - 62% and electricity saving of 62-70% respectively.
03
Opting for Dope-Dyed Yarns
Fabric
Waterless Color System Technology from e-dye
Image credit:ISPO Textrends
For synthetics dope dyed/solution dyeing is a water-saving solution. For dope dyed yarns, in bio, recycled and conventional polyester, nylon and spandex, the color batch is applied at the extrusion of the yarn. The benefits of this is that you get an even surface with barely no rejected fabric, as an even colorway is achieved. With the exclusion of traditional dyeing process, the water saving is significant.
ECLO is an innovative dope yarn technology awarded by ISPO Textrends, offering a high level sustainable polyester fabric for outdoor and fashion industry with excellent colorfastness.
Combined with the newest AIRSHIFT nano-membrane, the fabric releases double times breathability and storm waterproofness as well as great air permeability. The fabric is perfect for outdoor garments.
Leading polyester yarn supplier, e.dye, offers their Waterless Color System Technology for polyester. Requiring 85% less water, 90% less chemicals and 12% less CO2 emissions compared to traditional piece dyeing, the range of colors available is appealing.
The colored yarn displays high color fastness with no migration so contrast color-blocking can be easily adopted into design without potential risk, with contrasting colors in jacquards and intarsia structures guaranteed to remain fixed.
FENC has incorporated solution dyeing processes for its carbon capture polyester. The world’s first waste gas reuse technology, cooperation with Lanza Tech captures CO2 released from steel factories, converting the waste gas into ethylene glycol and polymerizing it into polyester. Accomplishing CO2 negative and reducing GHG emissions by 24% by combining Solution Dye Tech to skip the dyeing process, the products save 61% water, energy consumption is reduced by 67% and reduce GHG emissions by 85%. By incorporating the solution dye process, fabrics result in better sunlight protection, less discoloration and improved washing fastness than the traditional water dyeing process
Attached link
https://www.ispo.com/en/news/trends/how-textile-industry-reduces-its-water-footprintTaxonomy
- Textile
- Fibers & Textiles
- Textile